Compliant chemical plant storage streamlines operations while protecting workers, surrounding communities, and the environment. Routine product inventorying and segregation prevent incompatible materials from inadvertently interacting, creating toxic, volatile, and easily combustible mixtures that render undue harm and property damage. While storing hazardous materials by hazard class prevents and mitigates outsized storage risks, continuous onsite protection in steel-gauge chemical storage lockers provides comprehensive compliance and protection. Safe storage practices are never limited to the storage area, as a team effort is necessary for communicating potential threats and training all employees in safe protocols in hazmat events. Proper chemical labeling and ensuring all containers remain closed while not in use allows timely references by emergency response personnel during fires and plant emergencies. Secondary spill sump containment completes overall site safety by preventing leaks from compromised containers from polluting the environment and harming staff.
Noncompliant chemical storage invariably ends in disaster and lost profits. A Canadian chemical event tested the resolve of firefighters this week as crews scrambled to contact plant managers concerning the hazard class stored at the factory. Although water and common dry suppressants are ideal for fighting most fires, certain inorganic compounds and oxidizers react negatively with hydrant water. Subjecting firefighters to chemical infernos without proper suppressants and personal protective equipment, like respirators, poses immediate dangers to rescue crews. Although firefighters responded quickly, they were shocked to learn that the facility produced boiler chemicals and windshield wiper fluids, which require specific chemical compounds to extinguish. The fire chief exhausted all immediate first points of contact at the plant. As the fire raged on, no one at the facility could provide a complete list of the dangerous chemicals kept at the plant. The phantom onsite chemical list later materialized after the fire. Fortunately, the plant had a diminished chemical payload on site, but another danger persists.
Chemical Plant Storage Secondary Containment
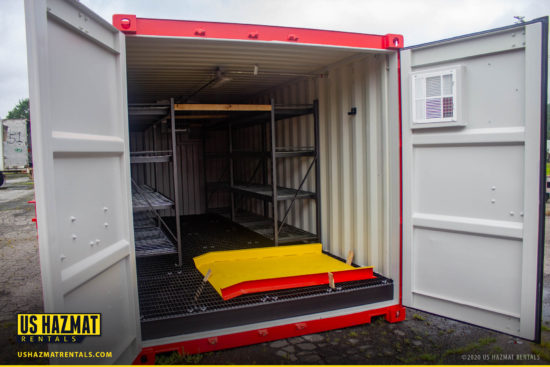
Secondary containment prevents spilled chemicals within a storage locker or designated warehouse from spreading to nearby operations, staff, and the environment. Runoff from the plant fire seeped from the facility before staining a nearby creek green. Contaminated water pooled in a nearby retention trench. A mobile chemical lab later determined the mystery compounds seeping into nearby water tables were volatile inorganic compounds. Onsite chemical plant storage with secondary containment and a sump could’ve prevented the compromised chemicals from breaching vulnerable property and ecosystems. Each US Hazmat Rentals’ steel-gauged chemical storage lockers comes with a bottom-affixed sump containment system, which sits beneath the standard steel-grated flooring that allows hazardous materials from breached or spilled containers to safely collect in the sump until safe extraction.
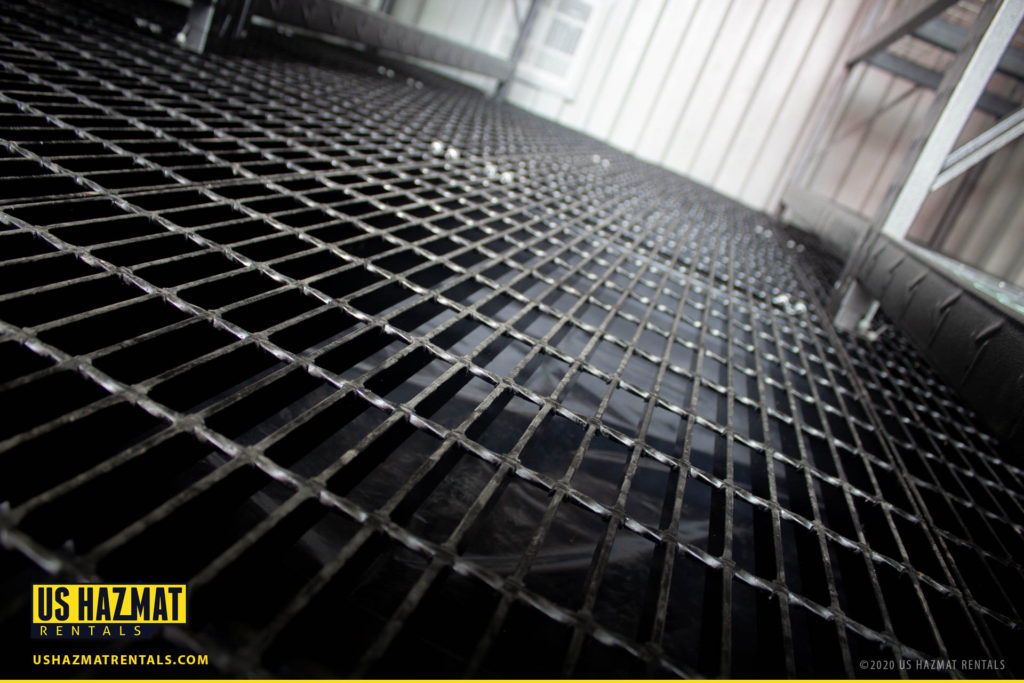
Segregate Hazard Materials By Class
Inventory managers should prioritize most dangerous chemicals onsite before moving and segregating dangerous chemicals in OSHA compliant storage locker. Pyrophoric chemicals (which ignite spontaneously) should be stored according to their pyrophoric properties, even if they are also flammable. Flammable liquids and oxidizers should be stored separately to prevent dangerous reactions.
Common Storage Guidelines
- Keep storage areas free from clutter, explosives, and flammable conditions.
- Prevent chemical storage conditions that may encourage rats or pests.
- Place stored materials at least six feet from hoistways and at least 10 feet from exterior walls.
Proper Chemical Labeling Saves Lives
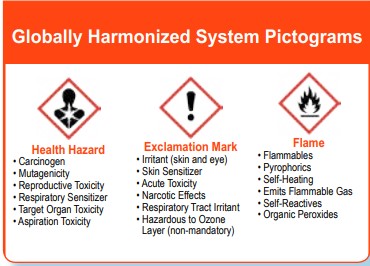
Although compliant chemical plant storage optimizes operations, it also saves lives. Engineers and foremen should always ensure all hazardous materials receive proper labeling for site delineation and application before storing when not in use. Moreover, employers must ensure clear and informative labels are affixed to all containers, including the chemical name, hazard pictograms, and safety precautions. Each facility must also keep a material safety data sheet for each dangerous chemical stored onsite. Safety data sheets contain detailed information on chemicals that describe its physical and chemical properties, as well as any possible health hazards of that chemical and what to do if inadvertently exposed to it.