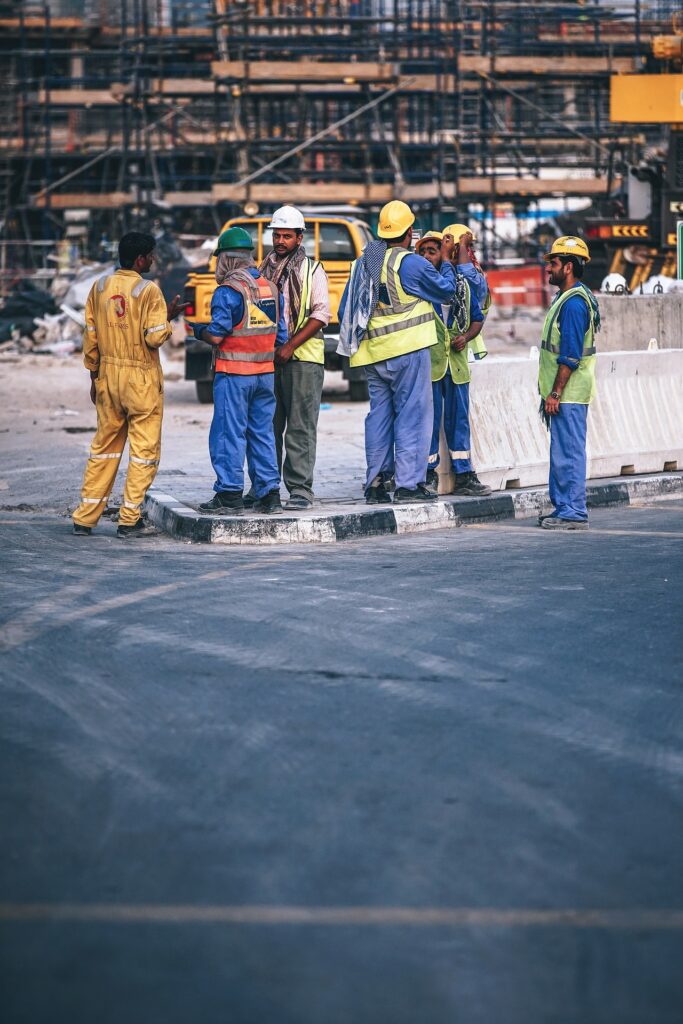
Rules. Rules. Rules. OSHA has rules and regulations for every industry. Failure to abide by stringent regulations will result in an unexpected visit from a compliance officer. But why is this federal agency so obsessed with regulations and basic safety standards that even a neanderthal could make sense of? Increases in worker compensation claims from careless accidents on the jobsite continue to plague modern industry. While safety standards and expectations surpass the dreadful working conditions of the early stages of the Industrial Revolution, workplace accidents remain in the range of unacceptable. OSHA now has a standard for every construction and general industry. And you can guarantee that if a rule is put into place, federal inspectors will come by to make sure you follow it verbatim. To help prevent workplace accidents and cultivate a positive working environment, develop a safety training program to curtail behavior that is as toxic as the chemicals you handle. We also have compliant chemical storage to help you with that as well.
Who is Responsible for Administering a Safety Training Program?
When it comes to workplace safety, employers must take into consideration every possible risk and hazard at the workplace. Making sure Billy Bob holds the ladder in place while another worker precariously hangs from the top rung while trying to retrieve a piece of roofing shingle that’s just out of reach of his overextended hand isn’t going to cover it. Risk assessment and mitigation must cover every possible hazard unique to one’s industry with complementary mitigation protocol to snuff out accidents before they happen. But it’s not just fallen debris from faulty scaffolding or unsecured tools that invariably will fall toward workers below. Federal regulations also contains volumes of rules relating to the storage of dangerous chemicals.
OSHA has a rule book and list of regulations that rival our nation’s tax codes. Understanding the convoluted language almost takes a Master’s in linguistics. Thankfully, there’s a cliff notes version of how to handle every potential toxic or hazardous material employees will encounter on the jobsite. Safety Data Sheets are the cheat sheets of industry. These sheets contain detailed information on the properties and associated risks of every applicable chemical use at your workplace. This condensed list outlines potential risks and hazards of each chemical and corresponding protective measures and how to handle hazardous materials. SDS have become an integral part of any safety training program.
How Much Training is Enough?
OSHA doesn’t always play the role of the boogeyman in enforcing standards and regulations. Federal investigators just don’t want to see anyone hurt. And it might be a cynical take, but federal administers have a vested interest in workers’ safety. Excessive accidents and worker injuries take a toll on the nation’s economy. Accidents slow down production and the number of available workers to make us competitive with China and other emerging super powers. It’s hard to grow the nation’s GDP if we don’t have enough workers to get the job done. Disability subsidies and worker compensation claims can also overstrain reserves and the national tax base. To assist with compliance, OSHA offers training outreach for workers and supervisors. The OSHA 10-hour training program is offered for entry-level employees, while the 30-hour program is geared for those who have safety responsibilities, such as supervisors.
Cultivating a Positive Working Environment
Careless behavior and shoddy attitudes can be as contagious as a bad cold. Just one sneeze or slip-up can befall an entire workforce, and you can guarantee company profits will take a hit, as well. If just one employee takes a lackadaisical approach to safety, such as tossing personal protective equipment to the side can have a ripple effect. Behavior is repetitious and bad habits can be tough to break. A safety training program can reemphasize and eradicate safety measures by holding both employers and employees accountable for their actions on the jobsite. Safety training programs can also boost employee morale by showing that you care and value each workers. This in turn can increase productivity and good will from the community you serve.