Storing large stockpiles of hazardous materials might feel like a herculean endeavor if you’re short on storage space. OSHA , following National Fire Protection Association guidelines – regularly enforce stringent regulations with unmatched bureaucratic efficiency. OSHA requires storage areas must be free of explosive or incompatible materials and stored in a dry and secure storage locker. Learning the lessons of previous chemical incidents, OSHA limits the storage of flammable or combustible liquids to 25 gallons in a room outside an approved storage container. OSHA also stipulates that no more 60 gallons of flammable materials with a flashpoint at or below 140 can be stored in an approved hazmat warehouse. Larger stockpiles are given special attention. OSHA requires no more than 120 gallons of combustibles with a flashpoint at or above 140 degrees can be stored in a hazmat warehouse. Allow us to meet your hazardous materials storage needs.
Compliant Hazardous Materials Storage for All Stockpile Sizes
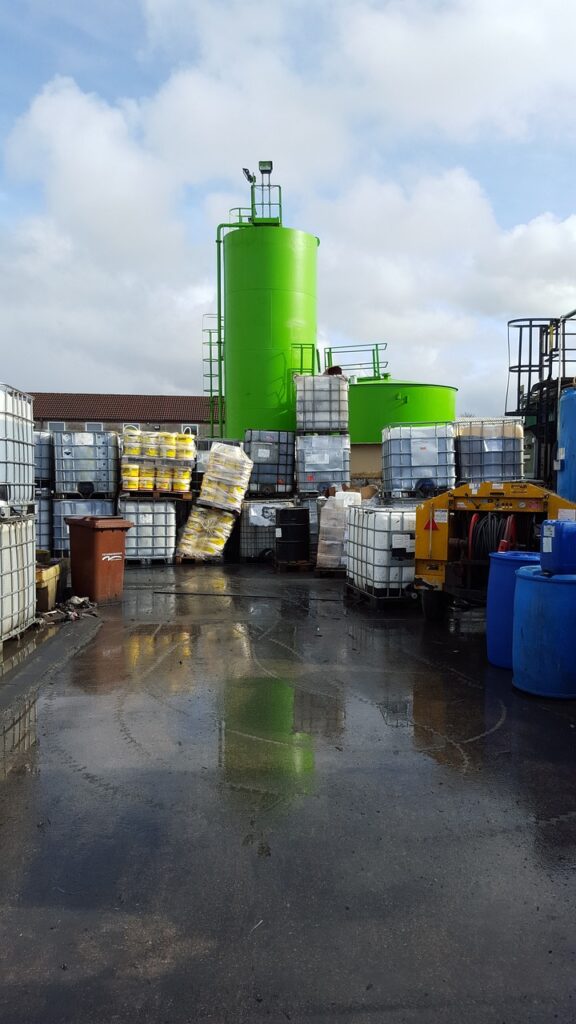
Although OSHA doesn’t stipulate metal structures as the preferred method of storage, steel presents enhanced protection. Our chemical storage lockers are comprised of thick steel sheeting and solid welds to ensure maximum protection for larger volumes of hazardous materials. Optional explosion relief can can also mitigate damage from contained blast radiuses. Although OSHA doesn’t require dry chemical fire suppression, we recommend this optional feature in preventing small fires from engulfing an entire manufacturing facility. Climate control and mechanical ventilation is ideal for larger volumes of hazardous materials. Accumulation of toxic vapors and escaping gases from flammable liquid storage drums and cylinders increase the chance of fires from errant sparks. Explosion-proof mechanical ventilation makes six air changes per hour at a rate of at least one cubic foot per minute.
NFPA 30 and 497 Compliance
Our two and four-hour fire-rated chemical storages meet all NFPA 30 and NFPA 497 rigorous safety standards. Although chemical fires and explosions receive the most publicity, spontaneous fires shouldn’t be your only concern. Leaks from inadequate chemical storage in unsecured lids can slowly lead to larger environmental pollution. Our innovative spill sump containment system mitigates the leak threats. During a chemical spill within the locker, the toxic substance will fall through a steel-grated flooring system, and into a sump until safe extraction. The NFPA also stresses the importance of proper chemical labeling. Chemical classifications in numbering and groupings determine the threat and magnitude of hazardous materials. These classifications also allude to the chemicals’ propensity for fire and destruction. Storing hazardous materials by correct grouping and numbering ensures continuous chemical compliance. Our hazardous materials encourage proper inventorying of dangerous and incompatible hazardous materials while allowing for better facility organization.
IBC Containers: The Unsung Heroes of Chemical Storage
Large volumes of hazardous materials should be stored in IBC containers or chemical drums. IBC containers are industrial grade containers commonly used for storing and transporting large quantities of liquids, solids, and semi solids. They are reusable and cost-efficient. Furthermore, IBC containers can be palletized, allowing for their easy storage and removal. IBC totes are commonly made of metal, plastic, or composite material. IBC totes are efficient as they are versatile and carry a maximum storage capacity of 330 gallons. Caged IBC totes are stackable, thus maximizing storage capacities. Metal alloy IBC tanks are engineered in compliance with NFPA and UL142 certification standards.
Metal chemical drums are another common and acceptable storage practice. According to OSHA Standard 1915.173, shipping drums and containers should never be pressurized to remove their contents. Drums and containers containing toxic or flammable liquids or gases shall not be stored or used where they are subject to open flame, hot metal, or other sources of artificial heat. Moreover, OSHA says “drums and containers of 30 gallon capacity or over containing flammable or toxic liquids or gases are to be placed in an out-of-the-way area where they will not be subject to physical injury from an outside source.” Metal drums should also be closely inspected to ensure the absence of punctures and abrasions. Steel drum stacking configurations for flammable materials should not exceed a specific gravity of 1.5. Avoid drum overhang on palletized systems.
What Pallet Size Should I Use?
Most industry experts agree that a pallet size of 48″ x 48″ is an acceptable load dimension for four-drum pallet arrays. Furthermore, inventory managers should make special effort to stack drums one-high per pallet. Floor-stacked chemical drum stockpiles should be done so on a flat and even surface. OSHA regulations prevent the stacking of pallets more than 15 feet high. Product inventory should determine pallet configuration and height. You should also avoid stacking pallets in high traffic areas.
Roll-Up and Wide Swinging Doors Allow for Easy Storage and Retrieval
Not all chemical storage lockers can meet the demands of higher payloads. Although each U.S. Hazmat Rentals warehouse is comprised of solid steel welds, larger stockpiles require extra protection. Our larger chemical storage lockers allow for the customed placement of roll-up and wider model doors. Roll-up doors allow for the easy storage and removal of chemical drum pallets and rigid IBC tanks by forklift. Pushback shelving also creates maximized storage space for larger volumes of hazardous materials. U.S. Hazmat Rentals provides temporary storage solutions to your ongoing storage dilemmas. We can meet storage requirements for various sized stockpiles. Contact us today for a free quote and consultation.