One nasty byproduct of the Industrial Revolution is the growing prevalence of hazardous materials and pollution. While high-octane petroleum and powerful disinfectants increased factory productivity, our ecosystem became littered with carbon contaminants and viscous sludge, sterilizing microscopic food chains and siphoning drinkable water supplies. To curb wanton environmental destruction, the EPA stepped in to safeguard our rapidly depleting natural resources to prevent further degradation. Although ardent environmental legislation has lessened pollution pangs, a residual threat to America’s pristine beauty persists. In 2022, small businesses and corporate manufacturers paid almost $150 million in fines and restitution for violating EPA anti-pollution ordinances.
What are the Effects of Pollution?
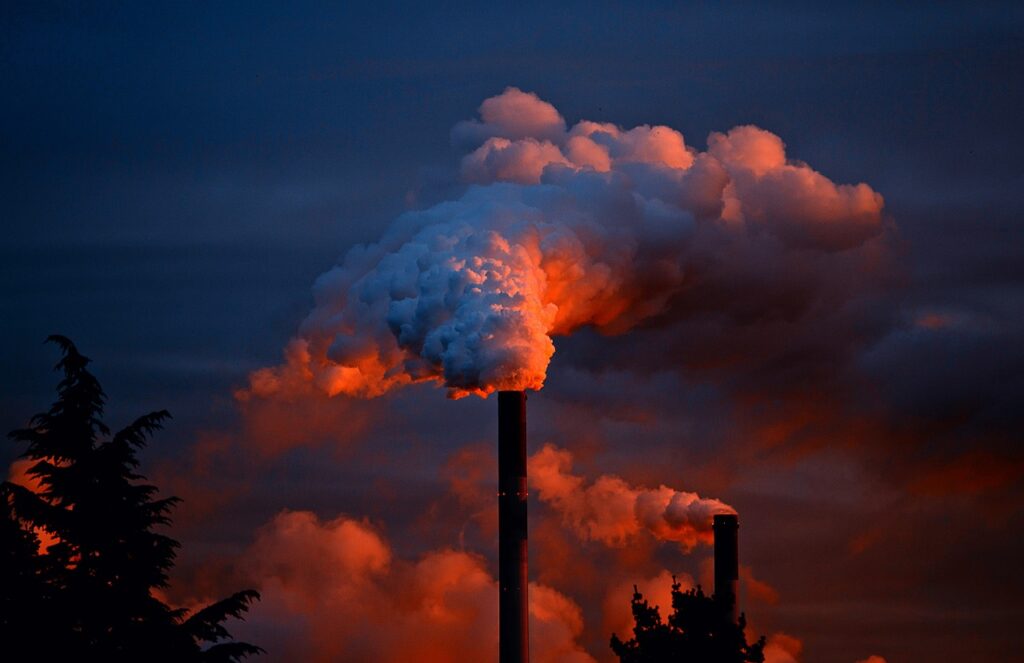
The effects of pollution on the environment are no longer up for debate. Climate Change is accelerating while negatively impacting life on Earth. Inadvertent pollution from negligible hazardous materials storage practices disrupts nature’s synchronistic harmony and delicate balance with living humanity that continues to exhaust its natural resources. Compliant hazardous material storage can help diminish residual environmental pollution.
How Has Chemical Storage Changed Over the Years?
Compliant chemical storage continues to evolve. From haphazardly built wooden storage sheds to sophisticated steel fortresses equipped with the latest safety features, compliant storage protection is no longer a nascent incarnation or frivolous expenditure. However, the advances in hazardous materials storage came with a steep learning curve. Industry progenitors couldn’t care less how an ailing planet would one day wither under pollution’s arrest. Mass discharges of toxic contaminants into vulnerable waterways were common practice in the early twentieth century with little regard to poisonous carcinogens and toxic precursors. While some of industry’s more altruistic conservators became early stewards of containment, the bulk of American manufacturers ignored common-sense storage practices while scoffing at the notion of environmental protectionism.
How Are Hazardous Materials Stored?
Accidental discharges of hazardous materials continue to cause irreparable harm to our ecosystems. Last year, the EPA reported 322 chemical incidents totaling billions of dollars in destruction. Although compliant chemical protection is always a phone call or click away, hundreds of renegade manufacturers run afoul of strict environmental conservation laws. Ignorance of the law is neither excusable or exculpatory. Today’s prevalence of plastics, composites, and steel drums provide EPA compliant hazardous material protection while ensuring jobsite organization and accountability. Our chemical storage lockers can accommodate large stockpiles of dangerous chemicals in IBC containers and smaller totes. Pushback shelving allows for easy inventory palletization while optimizing floorspace with turnkey storage. We also attach a sump containment system to every storage locker to prevent potential environmental incursions from escaping solid steel-welded technology.
Hazardous Material Storage and Employee Protection
Environmental protection isn’t the only reason we store hazardous materials. The United States is currently averaging one chemical accident every two days. Furthermore, EPA data reveals more than 1,600 accidents at facilities nationwide from 2004 to 2013. Currently, there are close to 12,000 facilities nationwide that carry or use hazardous materials that pose considerable risks to employees and surrounding communities. Oil refineries, chemical manufacturers, fertilizer industries, and waste management treatment facilities are a few of the more prominent industries handling highly toxic and dangerous chemicals daily. Chemical spills and hazardous materials incidents also necessitates the emergency evacuation of hundreds of thousands of temporary displaced residents annually. Our venerable chemical storage lockers meet all NFPA 30 and NFPA 30 Section 9.5 regulations in ensuring employee safety.
Determining Chemical Storage Needs
There’s no one-size-fits-all mentality when finding suitable and compliant chemical storage. What works for one industrial workflow or manufacturer will fail to meet OSHA, EPA, and NFPA regulations in another field. Furthermore, not every chemical stockpile will require the same level of protection within the same facility. Certain chemicals like ethanol and combustible liquids require fire-rated protection, while a non-fire-rated storage locker is acceptable for acids, bases, and corrosive liquids. Failure to secure compliant chemical storage can result in egregious penalties and potential workforce injuries. Our experienced and knowledgeable building advisors can evaluate your chemical storage needs astutely before presenting a list of affordable options. Contact us today for a free quote and consultation.
Hazardous Materials Storage Training
Proper employee education and training are the best tools in fighting non-compliant chemical storage practices. Each employee who handles hazardous materials should be trained on the necessary precautions for storing and retrieving dangerous chemicals. Hazardous material safety data sheets should also be readily available for each dangerous chemical found at your jobsite. An MSDS provides concise information on each dangerous chemical’s physical properties, known risks, first-aid measures, and storage guidance. Employers should also develop a safety preparedness plan for every possible emergency scenario. Employees should rehearse disaster drills regularly to ensure safe working environments.