America’s workforce is evolving and adapting to changing conditions brought on by the COVID-19 pandemic. With the first slew of lockdowns forcing millions of employees to abide by stay-at-home orders, Zoom meetings and online scrums became the norm for businesses nationwide. As the more stringent protocols of the lockdown receded with de facto herd immunity, project managers were not so eager to order workers back to company headquarters. To their delight, profits were up and worker morale were at an all-time high. But how could companies sustain shareholder gains with no one leaving their homes to buy products? During the pandemic, listless Americans did what bored shoppers did best: they bought stuff online they didn’t need to ward off mental malaise. Flushed with fresh funds from stimulus package payouts, online shoppers clicked away at every Google ad that manifested itself on their Facebook feeds, once again, churning America’s powerful economic engine. Project managers took note and relented on any immediate plans to axe working remote norms – at least until profits began to dip again.
Working Remotely Helps the Bottom Line
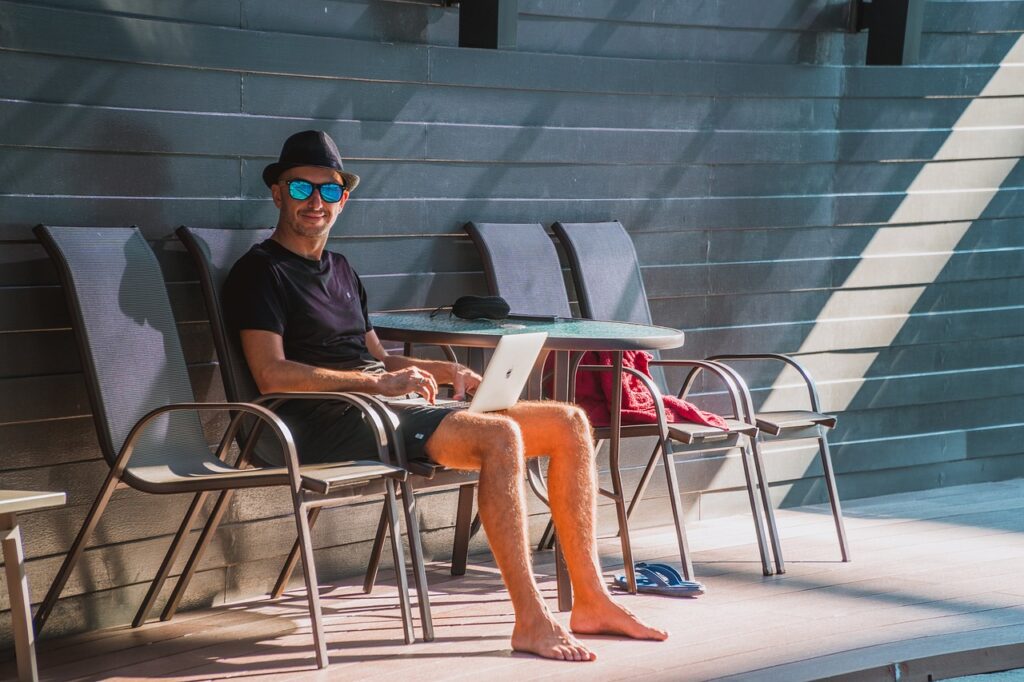
Soaring profits weren’t the only economic incentive for companies to continue working remotely. With productivity powering online sales, thousands of innovative companies ditched their brick-and-mortar locales as an online synthesis of apt project coordination and customer satisfaction negated the need for physical storefronts. While manufacturing facilities and shipping docks continued to rely on onsite manpower to complete orders, administration, sales, customer service and marketing personnel could continue to work at home. (Sorry, factory workers. But someone has to do the heavy lifting around here). Companies immediately reaped the rewards of evaporating overhead expenses and begin to divert the funds to other facility maintenance needs that had been neglected for way too long. One of those areas of manufacturing in dire need of “sprucing up” was compliant chemical storage. Every year, thousands of companies test fate by ignoring OSHA regulations pertaining to hazardous materials and employee training on how to handle dangerous materials. As a result, thousands of companies are ground zero for every chemical storage nightmare imaginable.
Employee Morale Feeds Organizational Growth
What do happy workers do when they don’t dread going to work? They tell their colleagues and friends, who then sing your praises to other professionals in the industry. If word gets around quick enough, you’ll never have to rely on headhunters again as HR’s inbox will become swarmed with the nation’s top talent looking to come aboard your steady ship that easily charts unprecedented financial waters. Business is like athletics: the best talent usually wins the most games, growing your fanbase, or in dollars terms, the number of customers. Like any sensible organization, you’ll invest in the team to keep the victories rolling. With soaring worker morale, employee retention won’t be a concern as you press forward on continuous quarterly growth. By keeping the best workers around, you can also weed-out lackadaisical employees who cut corners and hurt your team. Negligent or unhappy workers will always be a threat to companies. All they care about is just punching a clock and earning a paycheck. They couldn’t care less about quality craftsmanship, let alone chemical storage guidelines. Allowing employees to continue working remote will have a trickle-down effect and ensure your company is well-protected from chemical mayhem. With the added bump in dividends, you can avoid fines and finally invest in compliant chemical storage from U.S. Hazmat Rentals.